総額25億、年間売上額の2分の1にも及ぶ資金を投じたスマートファクトリー。
その新建設計画を託されたのは、31歳の若手だった。
会社の未来を 託されたのは 会社の未来を託されたのは 31歳の若手技術者
-
2006年入社 / 技術部 グループマネージャー 2006年入社 / 技術部 グループマネージャー 和歌山工業高等専門学校 修了片山 尚紀 Katayama Naoki
-
1992年入社 / 営業部 部長 和歌山工業高等専門学校 修了山本 洋之 Yamamoto Hiroyuki
-
1997年入社 / 製造部 部長 和歌山工業高等専門学校 修了永岡 悦三 Nagaoka Etsuzo
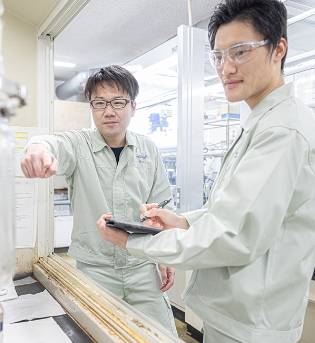
世界的な需要増を受け 製造能力の拡大が課題に
「任されたときの心境?涙なくしては語れませんよ」
と笑うのは、31歳(2016年当時)でFM2プロジェクトのサブリーダーを担った片山。総額25億。年間売上の50%近くを投じる、会社の命運をかけたプロジェクトが彼に託された。
1960年代から生産を続けているDHDPS。古くは染色助剤として、近年では耐熱性を持つスーパーエンプラ用モノマーに使われている主力製品だ。小西化学は生産量、品質ともに国内随一のDHDPSメーカーとして知られており、1972年には世界に先駆けて高純度品を上市。80年代には当時、世界最大級の化学メーカー、英国のICI社に製造技術ライセンスを販売している。
航空機(ボーイングが採用)やダイアライザー(透析装置)など、PES(ポリエーテルスルホン)の用途は年を追うごとに拡大し、その原料であるDHDPSへの需要も爆発的な広がりを見せていた。中国など海外メーカーが新規参入してくるのは時間の問題であり、価格以外で差別化を図らなければならない。
国内の競合他社、日本進出を狙う海外メーカーを寄せ付けない、競争力のある製品を造るには「今までにないDHDPSの生産体制」を構築する必要がある。そこで2016年に計画されたのが福井工場M2プラント建設プロジェクト(略称:FM2プロジェクト)
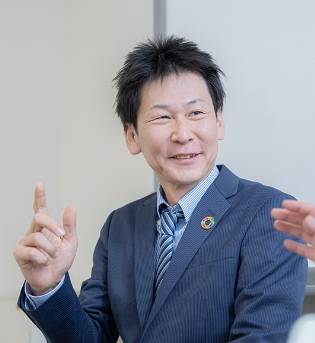
「和歌山(本社工場) にある第一工場の 「和歌山(本社工場)にある第一工場の コピーではダメだよ」 「コストは絞らないと」 「コストは絞らないと」
大先輩から寄せられる叱咤激励を受けながら、
- 自動化による省人体制
- 完全IoTを見越した新規技術の導入
- コンパクトかつ最小設備によるミニマム設計
3つのテーマをプランに盛り込んだ。
上記の課題をクリアするプラントは、設計を担当するエンジニアリング会社も経験がない。小西化学の社員が主要メンバーとなって、建物から取り組むのは30年ぶり。つまり、在籍している社員の中には経験者がいない。なにもかもが一からの挑戦だ。プロジェクトのリーダーは数々の実績を持つ取締役の平尾だが、立場上、多数の業務を兼務しているため、現場に張り付くわけにはいかない。実務上のリーダーは片山が担うことになる。「まさに五里霧中。10名弱のメンバーとエンジニアリング会社が試行錯誤を繰り返しながらのスタートでした」
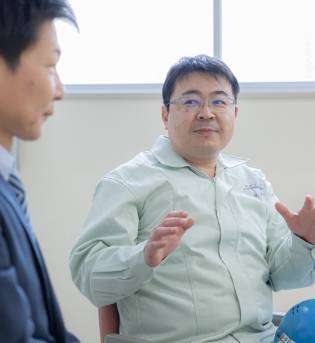
外観もスタイリッシュな スマートファクトリー
機能とデザインは、両立しないことも多い。それでも次世代スマートファクトリーを標榜するM2プラントは、設備面だけでなく“見た目”のスマートさにもこだわった。とくに外観デザイン優先で進めたのは、道路に面した東面。窓を一列並びに配置し、ガラリの出っ張りを抑え、ロゴも掲げた。
通常は鉄骨を組み、壁、屋根を施工してから内部に機械・設備を運び込むが、採用したのはジャスト・イン工法。機械を先に据え置き、その後に床・屋根・壁を取り付けるという逆手順の工法だ。設備の導入を担当した永岡は「機械の運び込みがしやすく、工期も短縮できる。一方、雨風を凌ぐための処置を施さなければならず、手間もかかる。建築業者と設備業者のスケジュールを管理していく煩雑さもあった」と振り返る。
全館に無線通信ネットワークを張り巡らし、タブレット端末による運転制御をめざしたM2プラント。
「最初は電波が安定せず、苦労しました」と永岡。1秒未満のスパンで蓄積していたデータを5秒ごとに変えると、動きが滑らかになった。ただ、不具合の原因は複雑で、幾つもの要因が絡み合って発生している。原因を特定して解決するというトライアンドエラーを繰り返し、一つひとつの問題を解きほぐしていった。
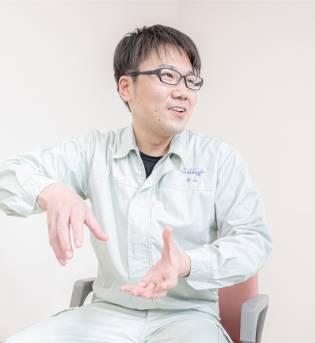
トラブル続出 使命感と皆の存在が励み
約2年後の2017年11月に工場が完成。12月4日から実液試製造を開始した。
顧客に約束した認定用サンプル30tonの提出期限は12月中。十分に余裕を持たせたスケジュールのはずだったが、想定外のトラブルが続発した。「機械の度重なる故障、あちこちで粉は詰まるし、溶剤も硫酸も噴き出す。毎日、いろんなことが起こって、期限までにサンプルを供給できなかったらどうしよう?というプレッシャーに押しつぶされそうになってました」と片山。
会社に行こうとすると、涙が止まらない。和歌山に帰りたい。それでもM2プラントに着いてみんなの顔を見ると「よし!がんばろう」という気持ちになった。
12月24日、試製造開始から3週間以上が経過していた。片山が夜勤で出勤した時点で完成していたのは未だ20tonだけだった。残り2日で10tonの製造を達成できるのか?「できるわけないと思った」。が、その後、「嘘のように」装置が廻り始め、25日早朝に約束の数量を達成。営業担当の山本も、ほっと胸を撫で下ろした。「社長から聞いたのですが、『小西化学は約束を守ってくれる会社だ』とお客様が褒めてくださったそうです。片山さんや永岡さんたちの苦労があったからこそ、その言葉をいただけたんですね」
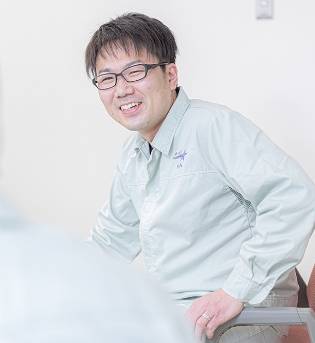
ボタン一つで動き出す 全自動システム
2018年3月から商業運転を開始。無駄を極限まで省いた仕様、現地採用した未経験オペレーターの技能教育をしながらのスロースタートとなった。
当初は設計上、可能な量の50%程度の能力しか出せず、機器のトラブルも相次いだ。設備担当の永岡も片山も「逃げたいという心境(笑)」。しかし、リーダーが真っ先に逃げるわけにはいかない。
トラブルのたび、粘り強く解析を行い、半年後には70%、1年後に80%、1年半後には100%へと着実に能力を引き上げていった。
M2プラントは、高純度のDHDPSを生み出すだけの製造施設ではない。小西化学らしいチャレンジ精神と、完全無人化を想定した先進技術が惜しげもなく盛り込まれた革新的な拠点である。
見学者が驚くのは、タブレット端末をクリックするだけで、全設備が連動して動き出す全自動システム。オペレーターが中央制御室に常駐する必要はなく、館内のどこにいても、たとえば食堂で食事を摂りながらでも槽内の温度や流量の監視・制御ができる。ヘルメットには小型のウェアラブルカメラが搭載され、将来的には画像解析型のAIと組み合わせれば、効率的な安全管理が実現する。QRコードを使った生産管理システムの導入により、原料の発注や物流の手配などをシステムが代行してくれるかも。
M2プラントのノウハウと志を受け継いだM3プラントも、2020年に運転を始めた。片山たち各メンバーはそれぞれの持ち場に戻ったが、プロジェクトを通して得たものは少なくない。
「やればできるんだ、とこれほど強く思ったことはなかった」と片山。100%の能力で稼働するM2プラントは、今や会社の売上の25%を担う主力工場だ。
「当初は、なんで自分たちがプロジェクトのメンバーに選ばれたのだろうと思っていましたが、今はよかったと自信を持って言える。得難い経験でした」と永岡。顧客との窓口を務める山本も「新たな取引先の開拓にもつながっている」と力を込める。
あきらめずに前を向いて進み続ける。そのしんどさと素晴らしさは、経験した者にしかわからない。「まだ無理だろう」ではなく、「やらせてみよう」と若手を起用する小西化学にはチャンスが溢れている。その中で夢が現実となり、世の中を変えていくのだ。
最後に「もう泣きませんよ」と片山は笑った。