化成品メーカーから、単体で機能を発揮するオリジナル製品を開発・製造できる機能性素材メーカーへ。 先人が築いてきたビジネスモデルのパラダイムシフトを担ったのは、入社2年目の若手研究者だった。
オリジナル製品を つくる、会社初の プロジェクト 挑んだのは、 入社2年目の若手 オリジナル製品をつくる会社初のプロジェクト 挑んだのは、入社2年目の若手
-
2009年入社/ 研究部 部長 熊本大学大学院 自然科学研究科 物質科学専攻 修了盈 智典 Mitsuru Tomonori
-
2011年入社/ 研究部 研究グループマネージャー 岡山大学大学院 環境学研究科 資源循環学専攻 修了坂田 和歌子 Sakata Wakako
-
2014年入社/ 研究部 研究グループチームリーダー 理学博士(有機化学) 東邦大学大学院 理学研究科生物分子科学専攻 修了豊島 拓也 Toyoshima Takuya
-
2020年入社/ 研究部 徳島大学大学院 物質生命システム工学専攻 修了田中 雄也 Tanaka Yuya
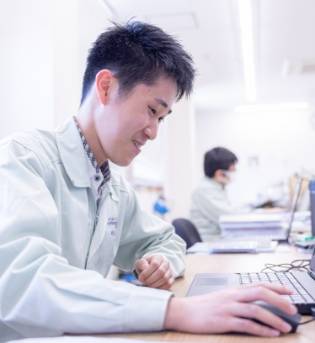
一度もやったことがない? だからやるんだ 一度もやったことがない? だからやるんだ
「成形?おもしろそう」
2021年春、入社2年目の田中は会社初の試みを任されたとき、そう思ったという。
長らく化成品メーカーとして知られてきた小西化学が、機能性素材メーカーへの転換を図るためには、乗り越えなければならない壁があった。そのための開発プロジェクトは田中の入社以前から進行していた。リレーに例えるなら、田中の役割はアンカー。運命を握る最終ランナーとしてバトンを受け取ったときに田中が抱いたのは、不安や重責感ではなく、内側から湧き上がる高揚感だった。
田中に与えられた業務とは、スルホン化ポリエーテルスルホン(S-PES)を使ったイオン交換膜の開発と製造、自社内での評価体制の構築。社内ではだれも経験がない上に、田中自身、大学院で学んだのは化学反応やバイオなど。電気も機械もモノづくりも経験がなく、一からのスタートとなった。
田中の奮闘ぶりを紹介する前に、まずは小西化学にとってS-PESがいかに重要な製品であるかを知ってほしい。
小西化学のお家芸といえるスルホン化反応の中でも、DHDPS(ジヒドロキシジフェニルスルホン)は、ノウハウがぎっしり詰め込まれた主力製品。DHDPSの製造において国内で右に出るものはいない、と胸を張って言える自信作だ。このDHDPSを原料に、スーパーエンプラのポリエーテルスルホン(PES)が作られる。PESは、その耐熱性や強度によりボーイング787の機体用材料の添加剤として採用されている。このPESを更にスルホン化したものがS-PESである。
つまり、S-PESは、小⻄化学の技術の結晶であるのDHDPSが顧客でPESとなり、小⻄化学のコア技術のスルホン化によって、さらなる高機能化を実現した商品なのである。
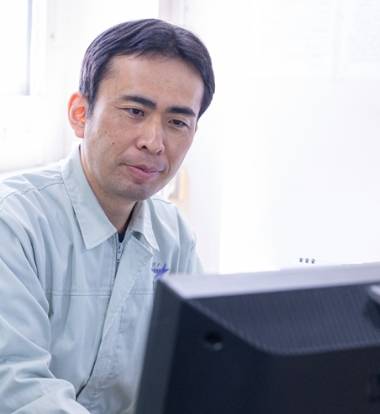
相反する性能をどう両立? 過去のデータから ヒントを発掘する 過去のデータからヒントを発掘する
ーーそもそも、小西化学のスルホン化ポリエーテルスルホン(S-PES)は、どのように誕生したのか。
ときは2011年に遡る。
当時、研究部のチームリーダーだった盈は頭を抱えていた。「顧客から、高スルホン化率と高分子量の両立という、本来トレードオフの性能を同時に実現してほしいと要望を受けていたんですよ」と盈。
S-PESは、ポリエーテルスルホン(PES)を濃硫酸で処理することにより合成される。が、この方法だと分子量が低下し、強度が落ちる。塩素系溶媒をスルホン化剤と併用すると低分子化は防げるが、PESが均一に溶けないため、反応物が取り出しにくい。こうした理由から、それまでのS-PESはスルホン化率は高いが分子量が低いもの、あるいは分子量は低下していないがスルホン化率が低いもののいずれかに限定されていた。顧客は水処理膜での用途を想定していたため、強度もろ過機能も維持できるS-PESを求めた。
ーー途方に暮れながらも盈は、過去のデータに立ち戻ることから始めた。
どの溶媒なら要望を満たせるのか。ていねいに再実験を重ねていくうちに、ある溶媒に行き着いた。「その溶媒を使うと、高スルホン化を達成しながら、PESの分子量が低下しない」。しかもPES、S-PESを溶解させることもできるため、工業化への見通しが立つ。
数ヶ月後にこの方法を見出したとき、盈は多くの研究者がそうであるように感情を排除し、「本当か?」と疑うことを忘れなかった。失敗だけでなく、成功したときの要因も慎重に検討する必要がある。さらに良質のS-PESが膜としても高い性能を発揮するとは限らない。喜びを噛み締めたのは、すべてを確認した後だった。
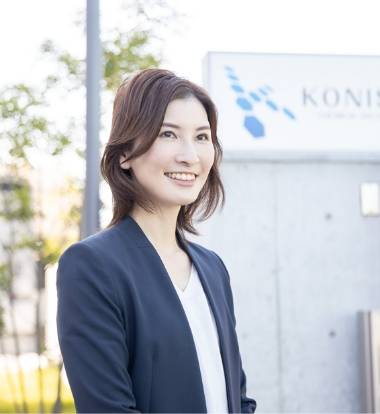
スケールアップの魔物~1 ラボ処方を確立してからが 本当の闘い ラボ処方を確立してからが本当の闘い
ーーチームのメンバーだった坂田は、完成したS-PESのスケールアップに向け、検討を始めた。
高分子のスルホン化という今までとはちがう様相の実験だけに、成功率は高くない。しかし、坂田には持ち前の明るさと責任感、そして周囲が舌を巻く行動力があった。
口数は少なく、手数が多い坂田。リズミカルにタスクをこなしていく様に、3年後輩の豊島は「すごい人。自分に同じことができるだろうか」と、驚いたことを覚えている。
ーー坂田が合成したS-PESのラボサンプルは、顧客の性能評価に見事合格。
水処理膜の改質剤として、高い性能を示すことが確認されたことから、スケールアップ製造を依頼される。そして2013年、初めてラボ処方の100倍スケールで製造を実施した。
パイロットプラントと呼ばれる、比較的大きな設備での製造は、実験室のフラスコで合成するのとは次元が異なる。このときも予期せぬ失敗に見舞われ、顧客の性能評価では不合格となった。やはりスケールアップには、多くの魔物が潜んでいるとだれもが感じていた。
しかし、失敗は成功への一工程に過ぎない。「製造記録を綿密に見直し、議論を重ね、失敗の原因を絞り込んでいきました」と振り返る坂田。仮説を立て、ラボで検証を行う。そのうちに、改善点が見えてきた。改善点をもとに仮説を立て、再びラボで検証する。
そんな日々が続いた2013年夏、ラボの1000倍という規模で挑んだ2度目のスケールアップは大成功を収めた。顧客にも好評で、要望通りのサンプル量を無事、納品。
別チームのメンバーも、オペレーターとして製造をサポート。いざというときは皆で協力し合う小西化学の風土が、スケールアップの魔物を追い払った。
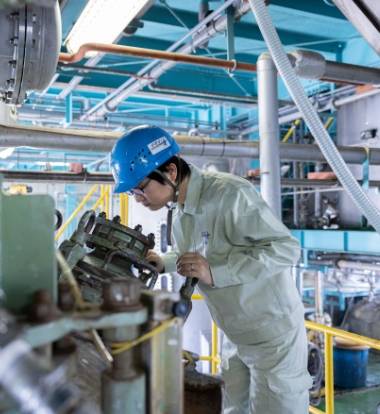
スケールアップの魔物~2 悔し涙とともに リベンジを誓う スケールアップの魔物~2 悔し涙とともにリベンジを誓う
ーー2017年、別の取引先から新たなS-PESサンプルの要望が入る。
今度はパイロットプラントではなく商業用プラント、つまり実機での製造となる大口の依頼だ。
この大役を任されたのは、当時入社4年目の豊島。
スケールアップの経験はあるが、実機プラントは担当したことがない。S-PESを扱うのも初めて。初めて尽くしの豊島を同僚の面々がバックアップすることになった。
「パイロット設備のデータを用いれば実機でも上手くいくはず」と机上のデータのみで考えていたと語る豊島。
「このような甘い考えはスケールアップの魔物の恰好の餌食になると、痛感することになりました。」と苦笑する。
ーーパイロット設備と実機の最大のちがいは、造粒工程とろ過工程にある。
2014年にパイロットプラントで製造したときは100kgだが、今回の依頼は400kg。造粒・ろ過設備ともに実機製造用に準備したが、両方とも見事に失敗。得られた量は、目標の半分に満たなかった。
期間が延長した上に特殊な作業をすることになった現場オペレータにも、「多大な迷惑をかけてしまった」と豊島。申し訳なさと悔しさに涙を流しながら、リベンジを誓った。
1年かけてラボ検証を重ねつつ、ボトルネックだった造粒・ろ過工程の問題解決に取り組んだ。「小西化学には昔も今も、転んでもただでは起きないスピリットが根付いているんですよ」と力を込めて言う。
それから1年後、2回目の実機製造を実施。100%解決ではなかったが多くの問題が解決され、安定的な実機製造が可能となった。
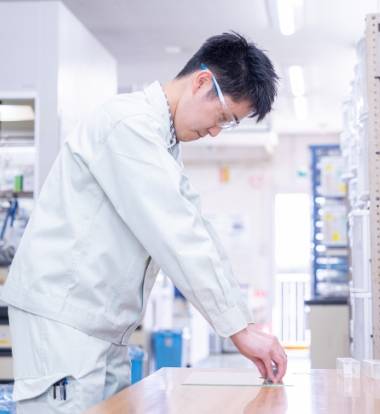
「これはチャンスだ!」 膜ビジネス市場に 躍り出る足がかり 膜ビジネス市場に躍り出る足がかり
ーーS-PESは開発の過程で、水処理膜だけでなく再生可能エネルギー用蓄電池のイオン交換膜としても有用であることがわかってきた。
だが、社内にはそれを評価する技術も機材もノウハウもない。これまでは外部機関や顧客が行っていたからだ。
機能性素材メーカーになるなら、自社で各種評価データを集め、製膜方法を確立しなければならない。その体制づくりと技術の獲得を託されたのが、入社2年目の田中だった。
ーー会社として前代未聞の分野だけに、教えてくれる人はいない。自身にも電気や製膜の知識はない。
そんな中で、田中は奮闘した。まず、S-PESをシート状に成形する方法を検討したが、「傾向はわかったものの目標にはほど遠かった」。膜の支えとなる基材には何がいいのか。これも社内にデータはないから、ネットや文献で情報を集めた。
焦りはあったが、同時に「チャンスだ」と思ったと話す田中。「これができたらブレイクスルーになる。難しい、いやできるかも、とあれこれ思いながらやってましたね」
ブレイクスルーに向けて、田中はこの分野で最先端を走る研究機関に派遣され、1週間で各種の評価方法を学んだ。
それを持ち帰ると、さっそくS-PESの製膜試験と性能評価を開始。しかし、同じ装置を使っているのに、再現ができない。わずかなセッティングのちがいが思わぬ結果を生むことを突き止め、坂田に負けないタフさで、田中は着実に壁を乗り越えていった。
ーー2021年も終わりに近づいた12月のある日、ついに高性能なS-PES膜の作成方法を発見する。
まだゴールではない。
量産には課題がある。が、小西化学が心血を注ぎ続けたS-PESは、カーボンニュートラルやSDGsといった、世界的なニーズに応え得る技術である。
その可能性に思いを馳せる田中の次なる野望は、この膜を大量生産し、売上に貢献すること。
「必ずやってみせます」。控えめながらも内側に熱い志を秘めた田中の眼差しにキラリと光が輝いた。